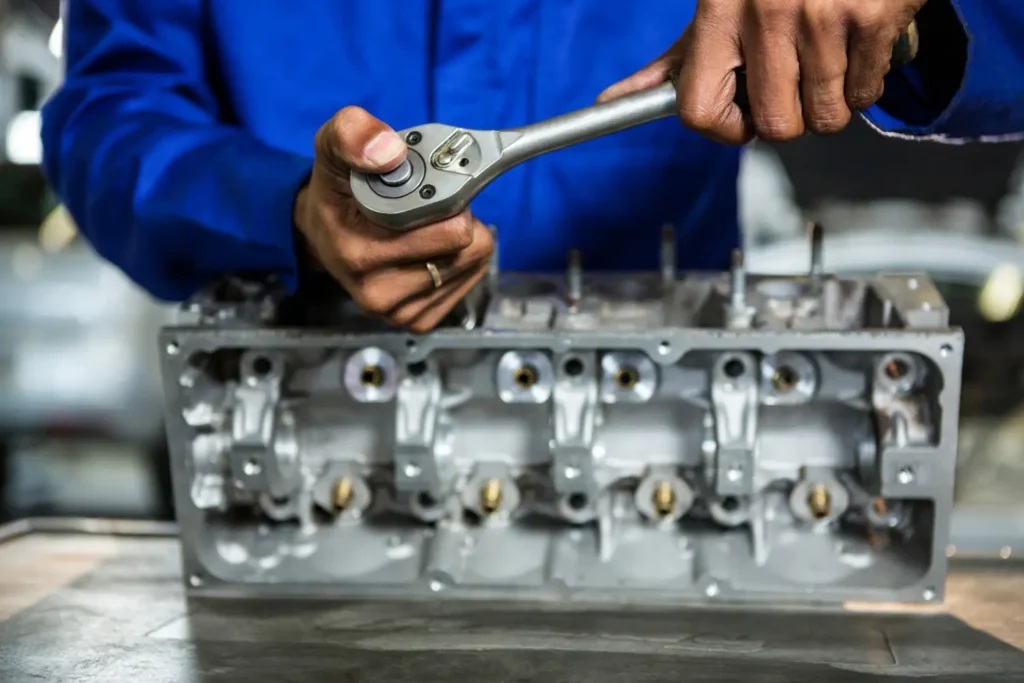
Types of Screw Compressors: Choosing the Right One for Your Needs
Screw compressors oil play a crucial role in the ever-changing world of industrial machinery. Screw compressors are well known for their efficiency and versatility. They come in various models, each designed to fulfill specific industrial requirements.
Screw compressors are becoming more common in the natural gas and refrigeration industries because of their superior dependability and high efficiency over other compressor types. Numerous advantages come with improved performance characteristics, including lower operating costs and a lower overall carbon footprint, both of which lessen environmental impact. Therefore, as screw compressor products and systems are developed, precise performance predictions are highly desired.
Types of Screw Compressors
Screw compressors are essential workhorses in the world of industrial machinery, boosting productivity in a variety of fields. Dry screw compressors and wet/oil-flooded screw compressors are the two main types of screw compressors. The rotors of both compressor types are closely matched.
Dry Screw Compressors: In dry screw compressors, there is no oil positioned in between the screws. A close-fitting pair of rotors installed in a cylindrical bore with tight clearance make up a dry screw compressor.
Wet/oil-flooded screw compressors: Oil fills the spaces between the screws in wet or oil-flooded screw compressors. A pair of closely mating rotors are also installed in a tight clearance cylinder bore in an oil-flooded screw compressor; however, the clearances for these compressors do not need to be as close as those for dry screw compressors.
How to Choose the Best Screw Compressor for Your Industry
Since screw compressor technology offers high-efficiency, low-maintenance compressed air solutions, it has completely changed the way many industries function. There are several things to take into account when choosing the ideal screw compressor for your industrial requirements. We will examine few essential factors to assist you in making a choice.
Capacity and Airflow: A screw compressor’s capacity and airflow dictate how much-compressed air it can generate and how quickly. It is essential to match the compressor’s capacity and airflow to the needs of your specific application to avoid paying too much or too little for extra capacity.
Operating Pressure and Duty Cycle: Because screw compressors are made to work in particular pressure ranges, it’s critical to choose one that can achieve the operating pressure you need. The duty cycle describes the frequency and duration of the compressor’s operation. The compressor’s duty cycle needs to meet the requirements of your application to ensure dependable and consistent performance.
Energy Efficiency: When choosing a screw compressor, energy efficiency is an important consideration. Highly energy-efficient compressors can drastically lower running expenses. The compressor’s specific power, or the amount of energy used per unit of compressed air produced, can be used to calculate energy efficiency.
Maintenance Requirements: Compared to other compressor types, screw compressors typically require less maintenance. However, regular maintenance is still needed to guarantee the compressor’s longevity and effective functioning. It is crucial to consider some maintenance requirements when choosing a compressor and account for them in your operating costs.
Noise Level: Compared to other compressor types, screw compressors operate at a lower noise level. Noise levels, however, may still be an issue in some industrial settings. It’s crucial to consider a compressor’s noise level and whether it will work well for your application before making your choice.
What Benefits Do Screw Compressors Offer?
Rotating screw compressors have many advantages over reciprocating compressors.
- They are ideal for large-scale applications because of their capacity to run at high airflow (CFM) and constant, continuous pressure.
- Reciprocal compressors have a maximum duty cycle of 60%, while rotary screw compressors have a 100% duty cycle.
- Unlike reciprocating compressors, which have more wearing parts and a higher heat-producing capacity, screw compressors remain functional throughout their long lives.
- Screw compressors have lowered energy and operating costs over time because of their excellent dependability and minimal maintenance needs.
Tips for Screw Compressor Maintenance
The workhorses of industrial processes and screw compressors require careful maintenance to maintain continuous efficiency. Here are some screw compressor maintenance tips to provide you with the knowledge you need to keep your equipment at its best.
- Frequent Examinations to Achieve Maximum Efficiency.
- Upkeep of Air Filters for Clean Performance.
- Keep an eye on and handle vibration problems.
- For a smooth operation, tighten any loose connections.
- Putting a Preventive Maintenance Schedule into Practice.
- When in doubt, seek professional assistance.
Conclusion
Gaining knowledge of screw compressor basics, such as how they operate and the differences between oil-injected and oil-free models, will help you make sense of the complex world these essential industrial tools inhabit. It’s important to carefully consider several factors when selecting the best screw compressor for your industrial needs, such as noise level, capacity and airflow, operating pressure and duty cycle, energy efficiency, and maintenance requirements. By choosing a compressor that satisfies your unique needs, you can raise the productivity and efficiency of your operations, which will eventually increase your profitability.