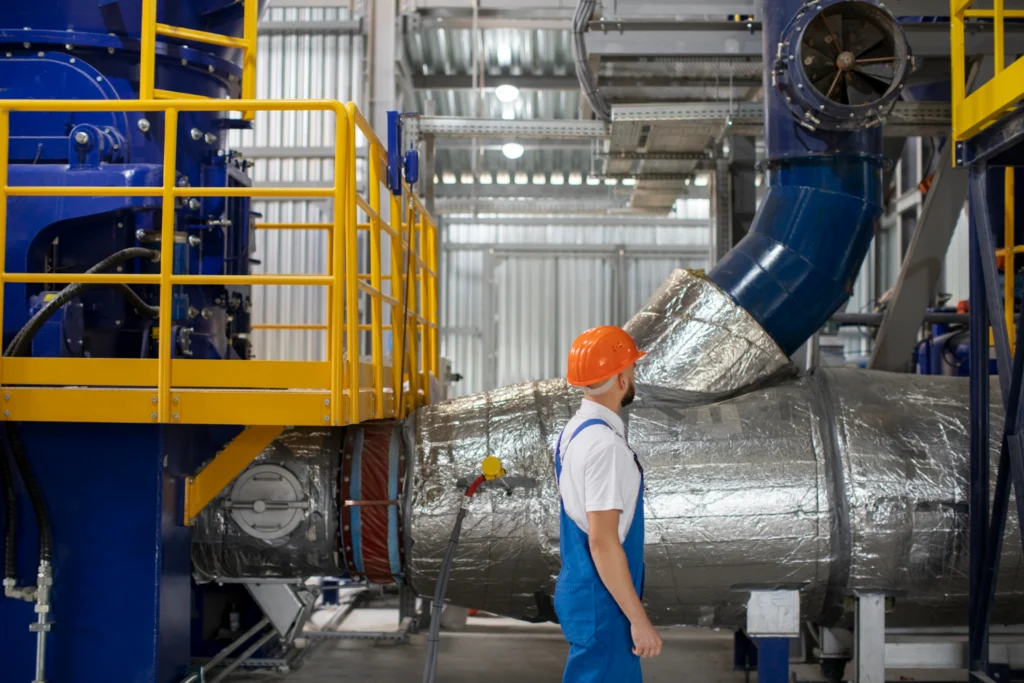
Understanding the Importance of Industrial Air Oil Separators in Machinery and Equipment
Industrial air oil separators are essential in many applications. These advanced devices support preserving compressed air systems’ integrity and efficiency. Industrial air/ oil separators extract oil, moisture, and other impurities from compressed air. Industrial processes frequently employ compressed air to power tools and machinery; moisture and oil can cause these equipment to be damaged and lower operational efficiency.
Why Air Oil Separation Matters
Air compressors cannot function without air oil separators. They prevent oil from getting into the system by helping to separate it if it is in the compressed air. It contributes to higher engine performance, which makes the machinery operate safer and more effectively.
Since air oil separators remove oil from the system before it builds up and causes harm, they also contribute to lower maintenance costs. Any air compressor arrangement would be complete with air oil separators, which must be routinely inspected and maintained for best results.
Numerous issues can arise from the failure of an air oil separator. In addition to higher oil consumption and exhaust pollutants, it can reduce fuel efficiency, PCV system failure, compressor element failure, and engine damage. It is essential to ensure that air oil separators are regularly inspected and maintained to prevent these issues to ensure optimal performance and fuel efficiency.
Benefits of Using Industrial Air Oil Separators
Industrial oil separators are robust devices used for various purposes that separate water from oil and other materials. For any operation handling hazardous materials, industrial oil separators are a necessary component.
These separators have the following advantages that can significantly enhance your facility’s performance:
Upgrade safety: The purpose of industrial oil separators is to lessen the possibility of explosions and fires caused by oil in a facility’s wastewater system. Industrial oil separators enhance facility and employee safety by lowering the possibility of mishaps.
Reduce energy expenses: By lowering the energy required to treat wastewater, oil separators increase profitability by lowering total operating costs. Because of the oil separator’s efficiency, fewer raw materials will be needed, which may result in cost savings.
Enhanced productivity: Industrial oil separators remove oil from wastewater and permit appropriate flow, increasing the facility’s efficiency. Eliminating surplus oil can lower maintenance expenses by requiring fewer cleanings and repairs. Furthermore, industrial oil separators can assist in reducing the energy expenses related to wastewater treatment.
Factors to Consider When Selecting an Air Oil Separator
Industrial air oil separators are essential parts of compressed air systems; they keep the system operating efficiently and safeguard expensive equipment by eliminating pollutants, oil, and moisture. To guarantee the longevity and efficiency of your equipment and procedures, choosing the appropriate air oil separator is crucial. Some factors to consider when selecting Industrial air oil separators are:
Flow Rate: The air oil separator that is chosen for the system must be able to handle the flow rate without creating inefficiencies. Selecting the appropriate size reduces energy usage and guarantees peak performance.
Filtration Efficiency: There are several designs available for industrial air oil separators, and each one offers a varying degree of separation efficiency. High-efficiency separators are required in industries. Make sure the option you select will meet your industrial filtration requirements.
Quality of Product and Reputation: The reputation of a manufacturer has a significant influence on the separator’s longevity and performance. Long-term cost reductions are frequently achieved by investing in reputable brands because of increased equipment longevity and energy efficiency.
Budget and Expenses: The most crucial factor to consider when choosing an industrial air oil separator is budget. Although sticking to a budget is vital, putting quality and efficiency first can save money over time.
Maintenance and Best Practices
Your industrial air oil separators can avoid costly repairs and costly downtime with regular cleaning. It will be beneficial to perform most routine maintenance checks daily or every week throughout the year, adhering to the preventative maintenance standards. Tips for maintenance of Industrial air oil separators are:
Inspections on Schedule: Set a schedule for routine inspections. Look for any indications of damage, leaks, or excessive oil accumulation in or near the separator.
Update Filter Components: The effectiveness of separation is greatly influenced by filter elements. As for replacing filter elements at the suggested intervals, adhere to the manufacturer’s instructions.
Clear or swap out the collapsing components: Over time, coalescing materials may become polluted. To preserve the best possible separation performance, clean them or replace them as needed.
Examine the Oil Levels: Keep an eye on the separator’s oil levels. To ensure appropriate operation, keep the oil levels as the manufacturer advises.
Instructions from manufacturers: Because they are specific to your separator’s make and model, always adhere to the manufacturer’s maintenance recommendations.
Conclusion
An integral part of every compressed air system is industrial air oil separators. They are essential in avoiding oil spills and loss, guaranteeing that the compressed air doesn’t become contaminated or carry over oil droplets. They are also necessary to keep the internal components of the compressor elements operating at peak efficiency. It is to make sure your separator is working correctly and offering your compressed air system the protection it needs; it is crucial to inspect and maintain it regularly.