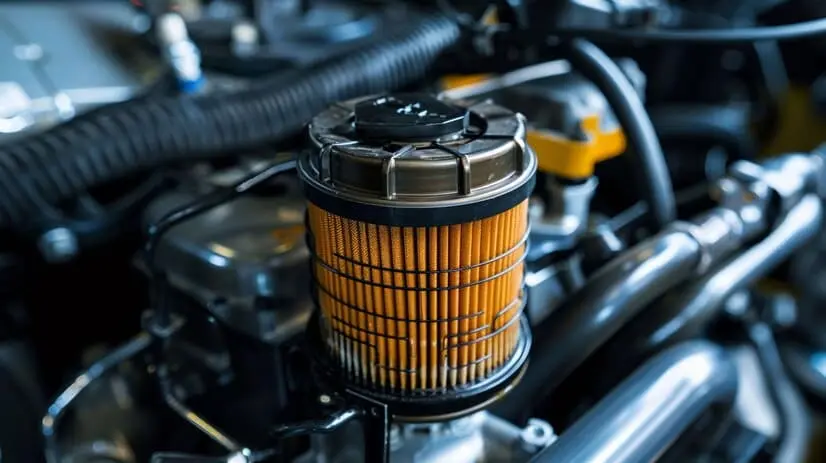
How Do I Know If Your Air Oil Separator Is Bad?
An air oil separator, sometimes called an oil demister, extracts oil from oil-infused air in engines, screw compressors, compressed air systems, and vacuum pumps. These separators are an essential component of the compressed air system and are vital to maintaining the intake system’s effectiveness and safety. Oil mist can lead to several problems without an effective separator, including decreased engine performance, more wear and tear on parts, and even system failure. These separators preserve the equipment’s longevity and efficiency by maintaining clean air.
Signs of a Bad Air Oil Separator
Understanding the warning indicators of an air-oil separator malfunction might assist you in resolving issues before they become serious. The following are some typical signs to be aware of:
Increased Oil Consumption:
The separator’s inability to effectively filter and separate oil from the air could be a sign of oil separator failure if you find yourself topping off the oil more frequently without any apparent leaks. This increased usage may result in higher maintenance expenses and even harm the compressor or engine.
Visible Oil Leaks: Although less frequent, you may observe seepage or leaks near the air oil separator unit. It is a sign of compromised equipment that requires repair. A malfunctioning oil separator may cause the crankcase pressure to rise, forcing oil past gaskets and seals.
Increased Pressure Drop: A sudden drop in pressure across the separator could be caused by a clogged filter element. Perform a thorough inspection, clean the filter element, or replace it if necessary.
Excessive Oil in the Air Stream: If oil is present in the air stream, this is a sign that the oil separator is not purifying the air well. An excessive amount of oil in the air might destroy components farther downstream and decrease your equipment’s overall performance.
Unusual Noises or Vibration: A malfunctioning air oil separator may also produce mechanical noise or vibration. If you observe increased vibration or hear strange noises coming from your equipment, it can be the result of a malfunctioning separator. These problems may impact your machinery’s lifespan and general performance.
Common Separator of Air Oil Problems
Various factors can impact an air oil separator’s performance. The following are some of the issues:
Clogged or Dirty Oil Separator: Dirt, debris, and oil can accumulate over time and impede the oil separator’s ability to perform its duty. A clogged separator can decrease the device’s efficiency, leading to a variety of problems, including higher oil consumption and decreased performance.
Worn or Damaged Gaskets: Seals are similar to gaskets found in your oil separator. However, If worn, fractured, or damaged, you will have a leak. When these gaskets wear out, your separator will become like a leaking faucet. Oil can escape, air can enter, and the system’s overall performance deteriorates.
Improper Installation or Maintenance: You must install and maintain air separators correctly for them to work effectively. Most need routine maintenance to ensure they effectively capture oil and don’t overflow or clog.
Separator Element Degradation: Utilizing an air oil separator for an extended period of time may result in the filter element becoming degraded. As it deteriorates, the element’s ability to properly filter air reduces, which affects the separator’s overall performance.
How to Prevent Air Oil Separator Problems
By keeping your separator of air oil functioning correctly, you can keep your equipment operating efficiently and save money on repairs. Here are some of the pointers to avoid problems:
Regular Maintenance and Inspection: Routine inspections and cleaning of the separator are vital to avoid potential issues. By performing routine maintenance, you may discover problems earlier and guarantee that the separator is operating as it should. Regarding maintenance intervals and procedures, following the manufacturer’s guidelines is essential.
Replacing the Separator at Recommended Intervals: The separator should be filled at regular intervals. In addition to ensuring that the separator continues to perform its functions efficiently, regular replacement can help prevent problems associated with filter degradation.
Proper Installation Techniques: When replacing the air oil separator (AOS), use original OEM (original equipment manufacturer) parts to ensure compatibility and performance. Correct installation is also crucial to the separator’s efficacy. Adhere to the manufacturer’s instructions to avoid frequent problems like leaks and inefficiencies.
Conclusion
Compressed air systems are only complete with oil separators as a vital component. In addition to ensuring that the compressed air does not contain any oil droplets or is not contaminated, they significantly reduce oil carryover and loss. Additionally, they play an essential role in maintaining internal systems, maintaining the efficiency of the PCV system, and ensuring that the compressor elements function correctly. Regular maintenance and inspection are very necessary to ensure that your separator is functioning properly and providing the required degree of safety for your compressed air system. It is true whether you are utilizing a spin-on separator or a cartridge-type system. Anand Filters provides premium air oil separators that are built to last and function at their best, guaranteeing the smooth operation of your system. We are the best in the industries, so trust us!